Hard Anodising

Welcome to Hard Anodising Surface Treatments Ltd, your UK leader in high-quality anodising services, particularly when it comes to anodising aluminium.
We’re one of the select few companies with the honour of holding a Hexavalent Chromium licence for Dichromate Sealing. This distinction empowers us to offer a comprehensive suite of hard anodising services, uniquely tailored to your precise specifications.
Benefits of Our Metal Finishing Services
Our metal finishing are recognised for their comprehensive coverage, technical superiority, exceptional customer service, and cost-effectiveness.
We provide:
- Comprehensive range of services:
Whether you seek aluminium anodising, aerospace anodising, automotive anodising, oil and gas anodising, OR motorsport anodising services, we have you covered.
- Comprehensive range of services:
- Superior results with Dichromate Sealing:
Our Hexavalent Chromium licence enables us to offer Dichromate sealing, vital for marine, oil & gas applications, and other sectors requiring anti-corrosion treatments.
- Superior results with Dichromate Sealing:
- Customised solutions:
We excel in achieving your desired coating thickness, colour, and technical properties for aluminium components, providing colour matching services. We offer both small and large component anodising, feel free to get in touch for more information.
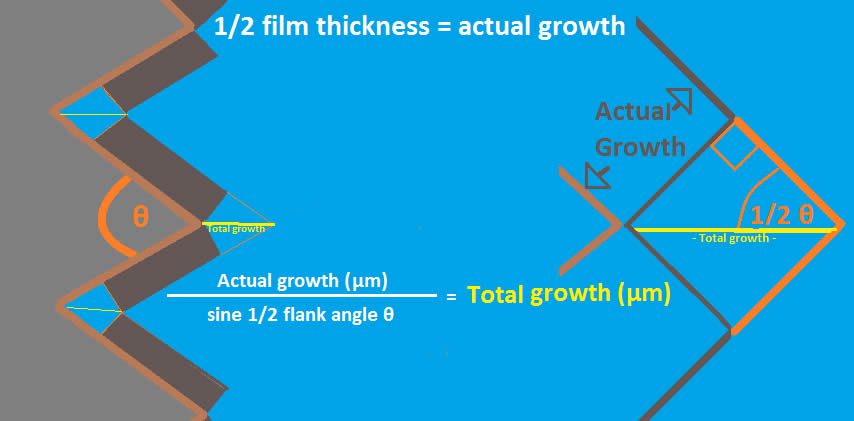
Reliable and High-Quality Metal Surface Treatments
Our reliable services offer a cost-effective strategy to increase the thickness of the naturally occurring oxide film on aluminium and its alloys. This process results in a coating akin to case hardening of steel, ensuring optimal technical properties.
The Impact of Hard Anodising on Dimensions
During the anodising process, the anodic film penetrates into and extends out of the metal substrate. It’s vital to consider half the coating thickness removal on pre-anodised faces to accommodate for buildup. Inward facing features, like internal diameters, will contract, while outward diameters will expand.
Understanding Colour Changes in Hard Anodising
Our hard anodising process yields darker coatings compared to standard decorative processes. The final shade is influenced by factors such as coating thickness, anodising conditions, alloy, and thermal history. While we control the anodising conditions, certain elements like the degree of hot or cold work are beyond our control.
Dichromate Sealing: Enhanced Corrosion Resistance
Our Dichromate sealing service further enhances our hard anodising offerings. This process involves impregnating our anodic films with a potent oxidising agent, ensuring optimum corrosion resistance.
The resulting colour can range from yellow OR green on sulphuric acid anodised films to ‘Nato Green’ on thicker hard films.
FAQs
What are the advantages of your Dichromate Sealing process?
Our Dichromate Sealing, enabled by our exclusive Hexavalent Chromium licence, offers superior corrosion resistance for components used in harsh environments like marine or oil & gas sectors. It provides a robust oxidising seal that improves longevity and performance.
How does it impact the dimensional tolerances of my components?
Hard anodising affects both the internal and external dimensions of components due to the anodic film growth.Typically, the dimensions increase externally and decrease internally. Planning for this change is essential, and our technical team can guide you on the precise tolerances.
Can Hard Anodising Surface Treatments Ltd match specific colours for anodised components?
When it comes to parts finishing, while hard anodising typically results in a darker finish, we offer customised solutions to match your specific colour requirements. The final colour can vary due to the aluminium alloy and anodising conditions, but our team can work closely with you to achieve the closest possible match.
What range of components are your services suitable for?
We can anodise parts for a diverse range of applications, including aerospace, automotive, oil and gas, and motorsports. We can handle various sizes and complexities, offering customised coatings for both individual parts and large batches.
How does Hard Anodising Surface Treatments Ltd ensure the quality and consistency of its anodising services?
We adhere to strict quality control protocols, utilising state-of-the-art equipment and processes. Our team comprises seasoned professionals who perform regular inspections and testing to ensure that every anodised component meets the highest industry standards and client specifications.
Anodisers Near Me
At Hard Anodising Surface Treatments Ltd, we strive to deliver reliable and high-quality anodised parts to meet your project’s specific needs.
Get in touch with our anodisers to discover how you can benefit from our aluminium anodising services.
Anodisers Near Me
At Hard Anodising Surface Treatments Ltd, we strive to deliver reliable and high-quality anodised parts to meet your project’s specific needs.
Get in touch with our anodisers to discover how you can benefit from our aluminium anodising services.